CFC RELEASES Another Powerful Addition to the Concept5 Product Formulation and Management Suite
Product Costing/Pricing System (CPS)
Product formulation, manufacturing, sales and delivery are common denominators in the retail formula feed production chain.
The right tools can assist management in accounting for a variety of aggregated costs, and in the development of competitive pricing strategies based on informed decisions.
Request Trial
Managers of profitable feed and food manufacturing companies must closely monitor the true production cost of a product from the creation of its formula through its delivery to the customer.
Achieving profit objectives and successful competition are predicated on the knowledge of accurate production costs.
Embedded in Creative Formulation Concepts' (CFC) Product Costing and Pricing System (CPS) is a host of comprehensive management tools that augment strategic planning. These tools equip managers with the current, detailed information they need about product costs and attained margins, when they need it, and are an invaluable resource in developing or refining pricing strategies and ultimately determining product profitability.
CPS is distinguished from generic bill-of-material product costing systems by its focus on the formula feed environment; the special needs of the animal feeding industries; and its bi-directional integration with the Concept5 least cost formulation system. The current Concept5 production formulas are used for rolling up product costs, and if desired, the costs computed during the ingredient cost roll-up may be updated in the Concept5 formulation database.
Multiple cost sets may be used to calculate the raw material cost of products based on alternate ingredient costs. This is a vital feature when basing the selling price of a product on different raw material costs, such as in forward/contract pricing.
Finished product manufacturing costs are computed rapidly and accurately. Flexible Cost Factors may be defined representing incurred costs at every phase of the operation.
Cost factors such as receiving; handling; shrinkage; grinding; rolling; mixing, pelleting, bagging, etc., may be defined at the system level with override capability at each manufacturing location (plant) and/or individual product.
Multi-level Cost "Roll-Up" applies the defined cost factors and computes incremental costs beginning with raw materials purchased outside - through premixes, concentrates and ultimately finished formulas.
Included in the Pricing function of CPS is an array of tools used to help establish product selling prices. Up to 50 selling price levels are available for computing selling prices based on rolled-up costs. The markup at each price level (wholesale, retail, dealer, etc.) may be defined as $/Ton and/or a percentage value, and may be applied to either the rolled-up raw material cost, or the computed selling price at another price level.
Since all direct and indirect raw material and manufacturing costs are reflected in the total product cost, markups represent exclusively the desired profit or attained margin. The distinction between actual margin, raw material and manufacturing costs is essential for accurate management of pricing strategies, and is lost when manufacturing costs are lumped together with pricing markups.
Final selling prices are rarely the result only of cost-plus-markup because of conditions such as market trends, competition, contractual obligations, and profit objectives. Within CPS, computed selling prices may be overridden manually, and summary reports reflect their impact on actual attained margins.
The Concept5 Product Costing and Pricing System is powerful management support software. It removes much of the guesswork, and assists in the development of competitive pricing strategies based on informed decisions.
Request Trial
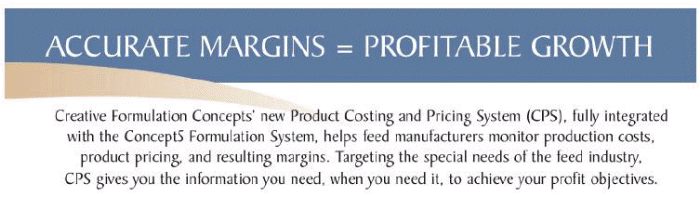
Concept5® and CPS® are registered trademarks of Creative Formulation Concepts
All rights reserved