
Product Costing
and
Pricing System (CPS)
What is CPS?
CPS is a powerful model that analyzes and reports product costing and pricing to give feed manufacturers accurate and timely information for establishing optimal competitive pricing strategies in a dynamic formulation environment.
CPS is management support software. Easy to understand and use, it is presented in a context familiar to the present-day needs of the animal feed manufacturer. Its bi-directional integration with the Concept5 formulation system and its outstanding formula feed features provide a focus and efficiency not available from generic bill-of-material product costing systems.
What CPS is not
CPS is not a replacement for feed accounting or enterprise resource planning software. Its purpose is to augment the use of such systems through bi-directional links to enhance production costing, pricing and profitability with unique functionality directly targeting the keenly competitive animal feed manufacturing industry.
Why “Cost-Price”?
Accurate margins equal profitable growth. Profit objectives, based on pricing strategies, are achieved when selling prices provide margins which will accurately and consistently meet ideal profit objectives. Decisions that may once have been based on an obscure conglomeration of expenses are supported on informed, computed selling mark-ups and standard prices. Current and previous period raw material costs, selling prices and several sets of costs are maintained and concurrently computed by a “cost roll-up”. Purchasing gain or loss differences between current raw material costs and selling prices and previous period raw material cost and selling prices are computed. Nothing is left to guesswork using the CFC Product Costing and Pricing System.
How CPS works
The typical feed/food manufacturer must account for a wide variety of costs directly associated with production. Costs in most manufacturing operations can be divided into three categories:
- raw materials
- labor
- manufacturing
Of the three, manufacturing is the more challenging as it comprisesallthe related costs of producing a product. Unlike raw materials and labor costs that are linked directly to the product, manufacturing costs must be linked through aprocess in a consistent, rational and logical manner.
There are indirect or fixed costs such as depreciation, advertising and promotion, administration, etc. that must be distributed over all products (or product groups). In addition to standard costs, there are numerous add-on production costs which may include raw material handling (receiving, unloading, cleaning, loss), processing (grinding, rolling, chopping, loss), mixing, pelleting, extruding, drying, packaging, distribution, commissions, etc.
In CPS, up to 125 of these add-on costs may be identified, representing direct manufacturing process costs of a raw material over and above its purchased cost. Each of these add-on costs is assigned a code, a name and a type. Once all standard and add-on costs are established, CPS quickly and accurately determinesallmanufacturing costs for each product at the plant where it is manufactured, from formulas stored in the Concept5 Least Cost Formulation database.
CPS provides what you need to know about true production costs allowing you to make informed decisions about your products' pricing that are vital to success.
How is so much information organized on the screen?
Click from the list below to view screen samples
Manufactured Product Cost/Price Details
Try CPS and Concept5 for 30 days with no obligation. Just double-click on “Profitable Growth” below and e-mail your trial request.
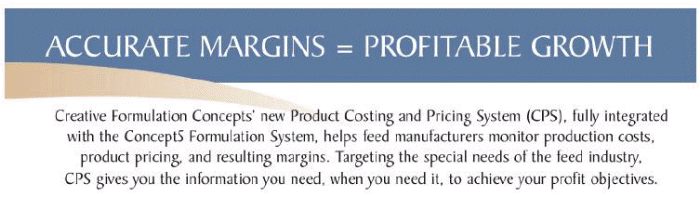